Introduction
Concrete, the backbone of modern infrastructure, cracks inherently—costly repairs and reduced service life. Self healing concrete changes this by embedding natural or engineered “healing agents” that autonomously seal micro-cracks, restore strength and extend a structure’s life. This article goes into the technical details, real world applications of self healing concrete work, and their future outlook, highlighting its self healing properties, a guide for engineers, project managers and material specialists.
Why Concrete Cracks and the Cost of Maintenance
Crack Formation Factors: Tensile weakness, shrinkage, temperature swings, mechanical loads and chemical attack all cause cracks in the cement matrix, leading to cracked concrete and disrupting the healing process .
Ingress and Corrosion: Even a 100 µm crack allows water, chlorides and sulfates to reach steel reinforcement, accelerate corrosion and spalling.
Repair Economics: Repair costs average US $147/m³—almost double the initial material cost (US $60–80/m³), making it imperative to repair cracks effectively .
Environmental Impact: Cement production contributes 6–7 % of global CO₂ emissions; frequent repairs add to this footprint.
Types of Self Healing Concrete: Definitions and Key Types
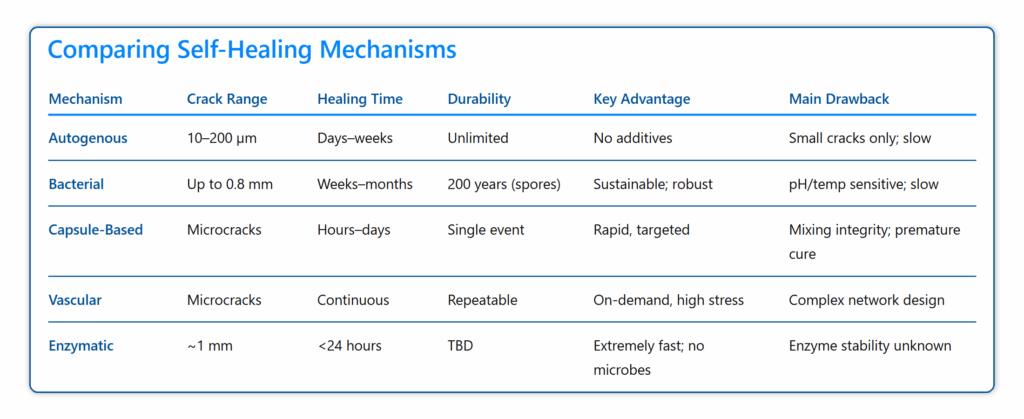
Autogenous Self Healing concrete process
This type of self healing concrete process, which employs a self healing mechanism, involves the hydration of unreacted cement particles and carbonation of calcium hydroxide (Ca(OH)₂) to form calcium carbonate (CaCO₃) to fill micro-cracks. However, its efficiency is limited to small cracks less than 300 micrometers wide and heavily dependent on water availability, making it crucial to fill cracks effectively.
Utilizes unhydrated clinker minerals and Ca(OH)₂ carbonation to precipitate CaCO₃ in cracks up to ~200 µm.
Pros: No additives; fully natural.
Cons: Limited crack width (<300 µm), slow (days–weeks) compared to normal concrete , requires moisture.
Bacterial Concrete
This type of self healing concrete process embeds bacteria, specifically Bacillus-type spores that, upon water ingress, produce urease to hydrolyze urea and precipitate CaCO₃, sealing cracks up to 0.8 mm.
Strains: B. subtilis, Sporosarcina pasteurii, B. cohnii.
Advantages: Spore viability up to 200 years; sustainable; repeatable.
Limitations: Weeks–months to heal; pH/temperature sensitive; carrier design critical.
Capsule-Based Systems
Microcapsules rupture on crack propagation, releasing polymers (e.g., epoxy, MMA) or sodium silicate, which react to form C-S-H gel or CaCO₃.
Pros: Rapid (hours–days); targeted delivery.
Cons: Capsule integrity during mixing; premature curing risks.
Vascular Networks
Embedded networks of tubes supply healing agents continuously; when intersected by cracks, fluid releases to seal damage.
Use: High-stress infrastructure (bridges, tunnels).
Challenges: Complex design; potential for clogging.
Enzyme-Enhanced Healing
This type of self healing concrete process incorporates carbonic anhydrase enzyme to catalyze rapid CaCO₃ formation from atmospheric CO₂ in cracks up to ~1 mm, thus demonstrating a self repairing concrete mechanism that achieves healing within 24 hours.
Benefits: Speed; no live organisms.
Unknowns: Long-term enzyme longevity in alkaline matrix.
Self Healing Concrete Process
Continued Hydration & Carbonation
- Water Ingress: Activates unhydrated C₃S and C₂S phases.
- CSH Formation: Fills micro-voids.
- CaCO₃ Precipitation: CO₂ + Ca(OH)₂ → CaCO₃, sealing cracks.
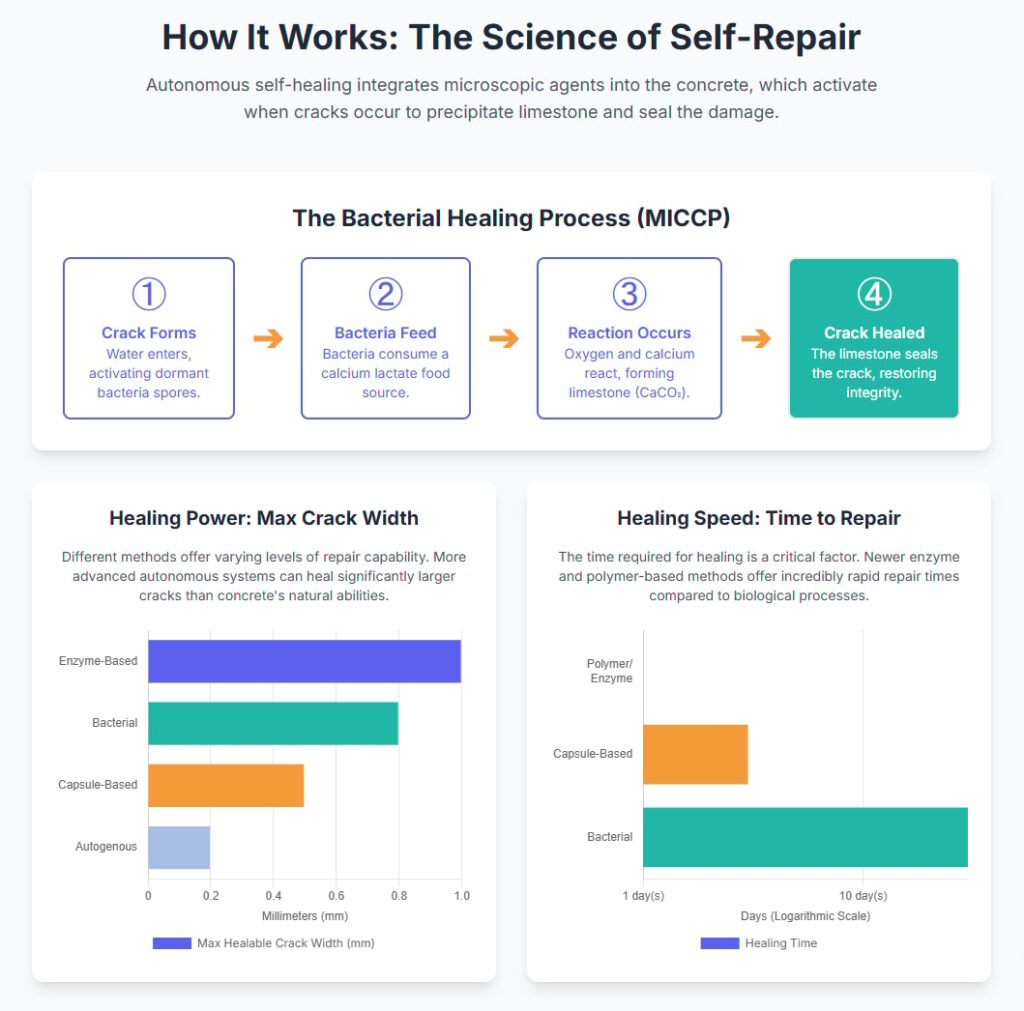
Microbially Induced Calcium Carbonate Precipitation (MICCP)
- Spore Germination: Water triggers bacteria.
- Urease Reaction: (NH₂)₂CO + H₂O → 2 NH₄⁺ + CO₃²⁻.
- Calcite Deposition: Ca²⁺ + CO₃²⁻ → CaCO₃ crystals at cell walls.
- Seal Formation: Gradual micro-crack infill.
Rupture-Triggered Release in Capsules
- Mechanism: Crack shear breaks capsules; capillary action draws healing agent into fissure; polymerizes or binds with Ca(OH)₂ to form C-S-H gel.
Enzymatic Carbonate Formation
- Catalysis: Carbonic anhydrase accelerates CO₂ hydration to carbonic acid and subsequent CaCO₃ growth on crack surfaces.
Recent Innovations and Technological Advances
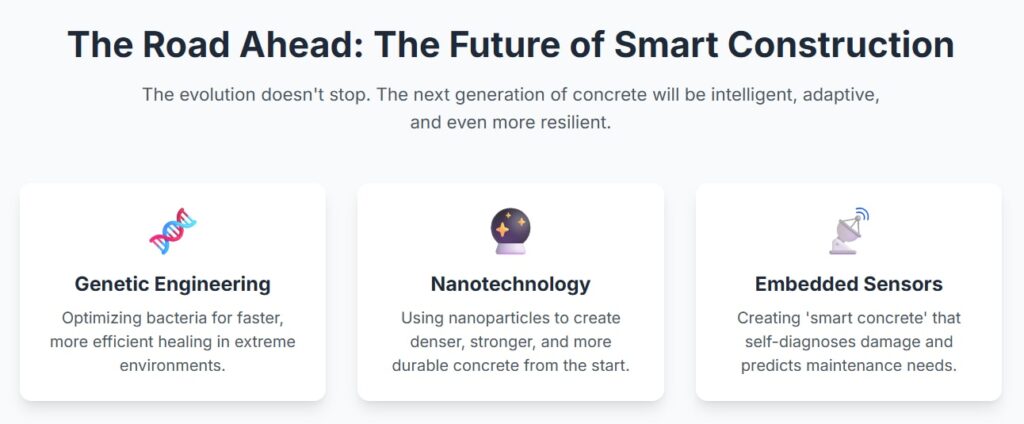
Genetic Engineering and Bio-Enhancements
Researchers are genetically engineering bacteria for higher urease enzyme output, enhancing CaCO₃ precipitation efficiency. Protective biofilms further extend bacterial lifespan in harsh concrete conditions.
Integration of Nanotechnology
Nanoparticles like silica and titanium dioxide increase density and durability, seal micro-cracks and enhance healing.
Smart Concrete and Real-Time Monitoring
Sensors in concrete enable real-time monitoring and predictive maintenance, increasing structural safety and proactive maintenance.
Implementations Across Globe
Europe
- Schiphol Airport, Netherlands: Bacterial concrete successfully repaired bus lane cracks, extending service life by over 15 years.
- M4 Bridge, UK: Reduced repair costs by 40% using microbial concrete, significantly minimizing disruption.
Asia
- Japan’s Basilisk HA: Mass-produced bacterial concrete effectively demonstrated crack sealing at New Chitose Airport.
- China: Plans underway to retrofit infrastructure in mega-cities with self healing concrete building for sustainability.
North America
- MIT Research: Inspired by ancient Roman concrete, utilizing lime clasts for durable, natural healing.
- PNNL’s Self-Healing Cement: Polymer-infused concrete capable of repeated repairs, increasing elasticity by 70%.
Economic, Environmental and Sustainable Future
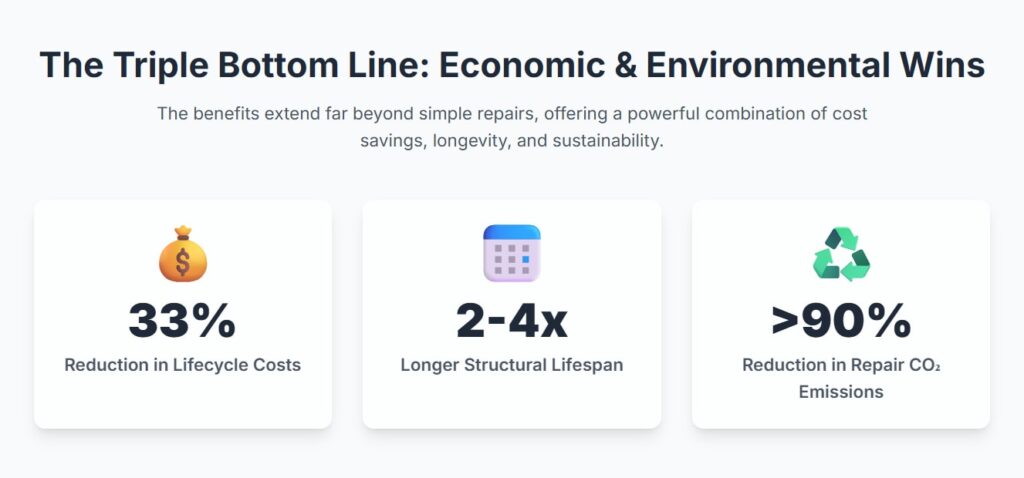
- Lifecycle Savings: Self healing concrete buildings can cut maintenance costs by ~33 % over 80 years versus conventional mixes.
- Extended Durability: From a baseline 20 years to 60–80 years, reducing early replacements.
- CO₂ Reductions: >90 % reduction in emissions from repair activities; halving cement-related CO₂ in high-adoption scenarios.
The autonomous repair capability reduces the frequent need for new concrete production, cutting CO₂ emissions drastically, aligning with global sustainability goals.
Challenges and Barriers to Adoption
Cost and Scalability Issues
High initial production costs remain a barrier, coupled with complexities in scaling manufacturing to meet global demands.
Regulatory and Standardization Needs
Robust standards and regulatory approvals needed for widespread adoption. Validation of long-term performance in various conditions.
- Upfront Cost: 10–30 % higher material cost deters procurement.
- Scalability: Specialized mixing, supply chains, and quality control needed.
- Standardization: Lack of codes and performance benchmarks delays regulatory approval.
- Long-Term Validation: Field data on durability under freeze-thaw, UV, and chemical exposure remain limited.
Conclusion
Self healing concrete is an innovative material and game-changer from reactive repair to autonomous maintenance. By incorporating natural and engineered healing agents – bacteria, enzymes, polymers – structures can self-repair cracks, reduce maintenance costs and CO₂ emissions. While cost, standardization and long-term data are hurdles, progress in biotech, nanotech and smart materials is driving adoption.